成功事例
原価低減を目指した生産改善
経営環境変化に耐えうる経営基盤の強化
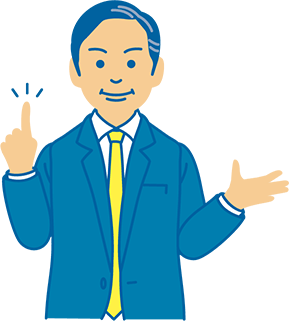
経営上の背景
外部環境要因
- ・食品原材料価格の高騰
内部環境要因
- ・食品加工事業への依存度大(約40%)
- ・既存の工場改善活動の低迷
- ・生産管理精度不足によるリードタイム長期化
解決プロセス後に得られた成果
生産平準化による食品生産工場部門の生産性改善と黒字化の実現、現場社員の行動意識の改善が図られた
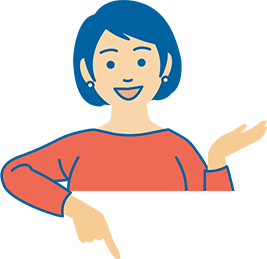
解決プロセス
「プロジェクト体制の構築と現状活動の問題整理」
目的
方針の共有と既存問題の認識
- プロジェクト体制の結成/工場長と若手の現場参加
- 現場改善活動の現状問題の再認識・整理
- ポイント
-
- ・現状の認識と問題の共有化
- ・
「改善活動の再計画」
目的
現場目線による
改善策の再設定
- 共通改善テーマ設定(5S)/目的と意識の共有
- 生産の現状再調査/生産・工程・作業分析
- 改善策検討と対策の試行
- ポイント
-
- ・個別作業要素毎の問題の詳細把握
- ・チームメンバーの情報共有、改善意識の共有
- ・
「多品種少量生産の仕組みへの展開」
目的
市場要求への対応力強化
- 平準化生産方式の検討
- 営業管理との連動性検討
- 標準作業・標準時間の設定
- 生産フローの整理と最適化の検討
- 実行計画策定と実行管理
- ポイント
-
- ・生産部門の部門改善だけではなく、全体最適化を目指し部門間連携を図る
- ・
企業概要
-
企業名
SB株式会社
-
事業内容
食品加工製造(ハム、ソーセージ)、卸、小売り
-
資本金
56百万円
-
従業員数
172人
-
売上高
7,949百万円(平成28年3月期)