成功事例
生産性向上と技術伝承基盤の確立
5S+S(安全)による職場改善と作業手順の標準化
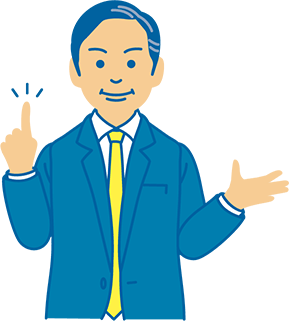
経営上の背景
外部環境要因
- ・震災後の防災予算増額特需の揺り戻し緩和
- ・消防車市場は購入予算減少による落札価格、数量は下落傾向
内部環境要因
- ・同社製品は国内最高性能として全国の消防自動車に採用
- ・震災による受注変動の経験から労務費削減に取り組むが外注加工費が増加
- ・後戻りやムダな作業の発生が生産性を阻害
解決プロセス後に得られた成果
確かな技術伝承の仕組みができるとともに、従業員のモチベーション向上にもつながった
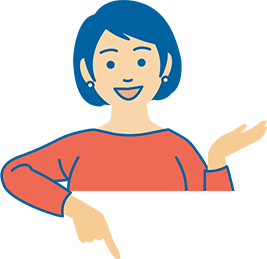
解決プロセス
「現状確認と課題抽出・改善」
目的
現状課題の解決
- 現状確認・課題抽出
- 改善提案シートとりまとめ
- 改善案検討と実施
- 改善効果検証
- ポイント
-
- ・自部署だけではなく他部署への改善提案を行うことで、より客観的な改善が実現できる
- ・
「作業手順の標準化」
目的
技術伝承に向けたスキルの可視化
- 作業の棚卸
- 伝承技能の特定
- 技能伝承の仕組み構築①年間計画②試験制度③技術活用状況の把握
- スキルマップの作成
- 作業手順の標準化①作業手順書作成②作業手順書の実作業での確認・改訂
- 作業教育訓練の実作業での実施
- ポイント
-
- ・スキルを細分化し、作業者ごとの保有スキルを明確にする。スキルを点数化することで、向上心を醸成し、多能工化に向けた活用を行う
- ・
「職場環境改善」
目的
6Sを導入した教育活動の実施
- 6S(5S+安全)教育
- 整理・整頓・清掃の実施
- ムリムダムラ撲滅活動の実施
- 安全教育の実施
- 効果検証と継続活動
- ポイント
-
- ・全社一斉に行う。不要なモノを捨てて、3定管理を徹底する。動線の見直しを行い、レイアウト変更も行う
- ・
企業概要
-
企業名
株式会社YK
-
事業内容
製造業
-
資本金
36百万円
-
従業員数
82人
-
売上高
1,841百万円(令和2年12月期)