成功事例
競争力強化につなげる
品質改善
グローバル市場で戦える生産体制づくり
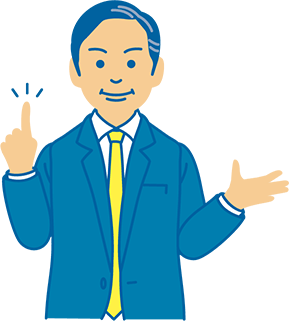
経営上の背景
外部環境要因
- ・対象市場(自動車関連)のグローバル化
- ・高精度金型ニーズや超硬材ニーズの進展
内部環境要因
- ・自動車関連市場での確かな実績
- ・高いQCDレベルの生産力
- ・技術革新への高い熱意
解決プロセス後に得られた成果
品質レベルの向上と品質改善のPDCAサイクルが形成され、作業者の改善意識が醸成された
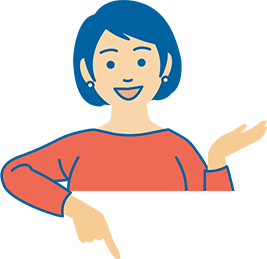
解決プロセス
「プロジェクト体制構築と意識共有」
目的
全社的改善意識の共有
- プロジェクト体制の結成/専務、製造部長、課長による全社体制
- 全員参加の意識共有
- 品質改善へのキックオフ/モチベーションUP
- ポイント
-
- ・全社改善に向けた一体感の醸成
- ・
「不具合の解析と標準化の推進」
目的
現状問題分析と
共通基盤の整備
- 不具合内容の分析/IE手法を用いた論理的分析
- 真因の特定
- 改善策の実施と月次管理
- 作業標準化の設定
- 技能評価基準の設定
- 技能向上策の実施
- ポイント
-
- ・現状の問題原因の徹底分析と対策検討
- ・標準的やり方や評価基準づくりで業務品質の安定をはかる
- ・
「重点不具合対策と部門内改善活動の推進」
目的
対策の深掘りと
改善レベルの向上
- 部門別改善テーマの設定
- テーマ毎のIE的分析
- 個別課題と目標の設定
- 管理方法の見える化
- 部門内PDCAの徹底(不良を自工程から流出させない)
- 技能教育の実施
- ポイント
-
- ・各部門の品質改善活動に展開
- ・品質問題の自責化、品質改善意識の浸透
- ・
企業概要
-
企業名
株式会社HD
-
事業内容
冷間鍛造金型の製造販売
-
資本金
30百万円
-
従業員数
134人
-
売上高
2,656百万円(平成28年6月期)