成功事例
製造現場の改善
(5S・ムダ取り)
製造現場の効率化と生産管理の仕組みづくりによる生産性の向上
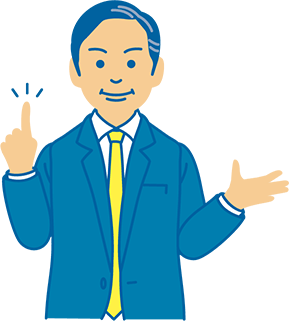
経営上の背景
外部環境要因
- ・国内市場は成熟し、低成長
- ・海外市場、海外ニーズへの対応必要性の増大
内部環境要因
- ・仕掛在庫の増加
- ・リードタイムの長期化
解決プロセス後に得られた成果
リードタイムが大幅短縮、生産性130%向上、年間1000万円以上のコストダウンが進み、過去最高利益に貢献
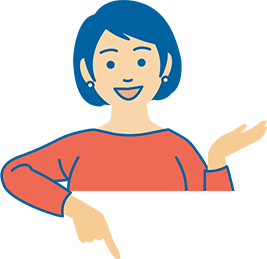
解決プロセス
「5S改善と3定の実践」
目的
現場改善の基礎づくり
- 5S活動実践/「整理」・赤札作戦
- 3定(定位・定品・定量)実践
- 5S活動実践/整頓・看板作戦
- 5S活動実践/清掃・日常清掃と清掃点検
- 5S維持・定着化
- ポイント
-
- ・現場改善の基礎作りとして、5S(「整理」・整頓・清掃・清潔・躾)と3定(定位・定品・定量)を実践
- ・現場の1人1人の意識付けが重要
- ・
「現場改善①」
目的
リードタイム短縮・生産性向上
- 生産の流れ化(ライン化、レイアウト改善により停滞・運搬のムダ取り)
- ボトルネック工程改善(前・後工程との同期化・作業方法の改善)
- 段取替え改善(段取り作業分析と改善)
- ポイント
-
- ・どこにムダがあるのかをまず「見える化」してから、ムダ取りの改善を進め、仮説検証として、改善効果の確認をする
- ・現場改善を進めるに当たって、小さな成功体験を繰り返していくことで、参加メンバーの自主性を高めていくことが重要となる
- ・
「現場改善②」
目的
不良削減・生産性向上
- 品質改善(QC手法で現状把握→ 要因解析→対策立案→実施→効果の確認→歯止め)
- 動線のムダ取り
- ポイント
-
- ・どこにムダがあるのかをまず「見える化」してから、ムダ取りの改善を進め、仮説検証として、改善効果の確認をする
- ・現場改善を進めるに当たって、小さな成功体験を繰り返していくことで、参加メンバーの自主性を高めていくことが重要となる
- ・
「現場改善③」
目的
生産性向上・定着化
- 人・設備の組み合わせのムダ取り
- 改善効果の確認
- ポイント
-
- ・どこにムダがあるのかをまず「見える化」してから、ムダ取りの改善を進め、仮説検証として、改善効果の確認をする
- ・現場改善を進めるに当たって、小さな成功体験を繰り返していくことで、参加メンバーの自主性を高めていくことが重要となる
- ・
企業概要
-
企業名
株式会社OR
-
事業内容
カッターユニット・産業用刃物・精密加工部品の開発設計・製造・販売
-
資本金
60百万円
-
従業員数
121人
-
売上高
3,300百万円(平成27年11月期)