成功事例
エネルギー消費量管理による
省エネルギー化
省エネ観点からの設備管理による生産効率の向上
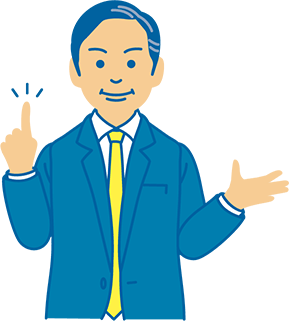
経営上の背景
外部環境要因
- ・東日本大震災による供給電力制限
内部環境要因
- ・設備メンテナンスが不十分
- ・ボトルネック工程のヒートロス
解決プロセス後に得られた成果
エネルギー管理体制が整い、組織的な対策により見込み以上の省エネ効果を得られた
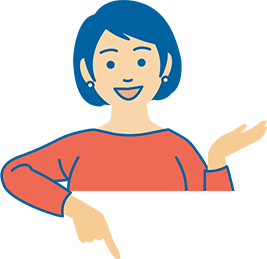
解決プロセス
「プロジェクト体制の構築と現状把握」
目的
課題の重要性認識と知識習得
- 経営者主導のプロジェクト検討体制の構築
- メンバーの省エネ目的と必要性の理解
- メンバーへの省エネに関する知識付与
- エネルギー使用設備の状況把握と問題把握
- 設備別エネルギー使用実態の定量化
- ポイント
-
- ・経営者主導でメンバーの重要経営課題の認識強化
- ・メンバーが自主的に省エネ活動のPDCAを回せるように知識付与を行う
- ・
「エネルギー使用量の見える化」
目的
全社的な方針と対策設備の
優先順位決定
- 他業界の事例収集と自社展開への検討
- 全社的な省エネ対策の方向性と目標効果の設定
- 定量分析による優先対応設備の検討
- モニタリングすべき定量的管理指標の設定
- 設備毎の省エネ対策立案と効果予測の算出
- 対策実行計画の策定
- ポイント
-
- ・他業界の事例の収集
- ・設備毎のエネルギー使用量の定量的管理指標の設定
- ・対策を実行すべき設備の優先順位付け
- ・
「段階的対策実行と継続管理」
目的
成果確認と自主的なPDCA
- 対策の実行①作業変更②管理方法の変更
- 対策実行設備の定量管理
- メンバーの省エネ成果の共有と重要性再認識
- 継続的な指標管理による省エネ活動
- ポイント
-
- ・設備投資不要な着手しやすい対策から段階的に実行する
- ・業務手順や管理方法の見直し・変更で生産性向を図る
- ・成果の定量的な確認と共有
- ・
企業概要
-
企業名
株式会社HC
-
事業内容
惣菜製造業
-
資本金
95百万円
-
従業員数
366人
-
売上高
4,533百万円(平成25年9月期)