成功事例
新工場への速やかな移転・
立上げ・安定生産
工場移転による生産能力拡大と新生産体制の構築・運用を目指す
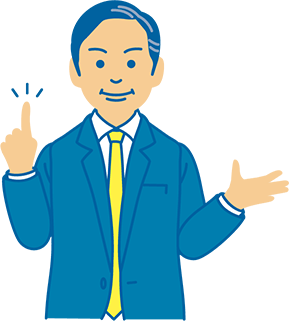
経営上の背景
外部環境要因
- ・中国など海外需要の拡大
- ・OEM製品の開発および販売要請
内部環境要因
- ・主力製品は国内市場で独占的地位を確立している
- ・中国市場向け出荷量の増大による生産力・在庫不足
- ・今後の受注増加に向けた生産・在庫計画見直しが喫緊の課題
解決プロセス後に得られた成果
創業以来の最高売上高を獲得でき、新生産体制に向けた製造部メンバーの実践的な理解の場となり組織力が高まった
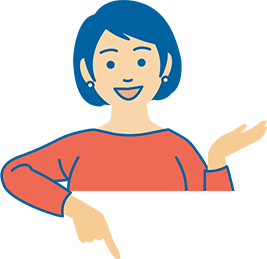
解決プロセス
「現状把握」
目的
生産体制の現状把握と問題点
及び課題の抽出
- プロジェクト体制の構築
- 生産・販売業務概要(業務プロセス)の把握
- 生産・販売実績の把握
- 工程フローと特性の把握
- ポイント
-
- ・現状認識と問題の洗い出しによるメンバー間の認識共有化と工程のボトルネックを検討する
- ・
「新生産・販売体制のモデル化と販売計画策定」
目的
受注増に対応できる必要生産能力の分析
- 生産能力分析①拠点別・工程別生産性分析/生産能力算定
- 適正在庫分析①全社・拠点別売上パレート分析/適正在庫分析
- 生産・在庫計画策定①生産平準化計画の試算②半製品・部材の在庫計画の試算
- 検討課題の洗い出し①課題の洗い出し②優先順位付け③対策案の検討
- 生産管理業務の見直し①生産計画編成②生産指示と実績管理③在庫棚卸等
- 運用体制の検討
- ポイント
-
- ・統計的な需要予測と受注のブレを見込んだ「シミュレーション」
- ・出荷予測と生産能力の対比
- ・設備増加に伴う人員計画の検討
- ・生産管理全般の見直しと見える化を図る
- ・
「新生産体制の承認と運用ルール設定」
目的
新ルール設定と生産シミュレーション
- 新生産体制案の承認①生産・在庫計画案の取り纏め②経営陣へ報告③生産・在庫計画の修正
- 生産基準類の整備①半製品・製品生産基準②部材発注基準
- 新業務の教育訓練
- ポイント
-
- ・全社での合意、生産計画策定のルール設定と定着化
- ・発注点・発注ロットの見直し
- ・
「新体制での生産開始、運用と評価」
目的
生産実行・管理PDCAサイクルの定着化
- 生産管理基準のメンテナンス
- 現行生産の課題の洗い出し
- 生産性評価指標の蓄積
- 運用評価
- 将来課題の洗い出しとその対策検討
- ポイント
-
- ・PDCAサイクルの定着化に向けて、組織的な管理体制を整える
- ・実績差異分析結果について対策を検討する
- ・
企業概要
-
企業名
株式会社KR
-
事業内容
製造業(理化学機器製造・販売)
-
資本金
40百万円
-
従業員数
48人
-
売上高
896百万円(平成30年3月期)