成功事例
生産性向上に向けた意識改革と
組織体制整備
改善効果の可視化と計画的人材教育で
改善PDCAサイクルの構築
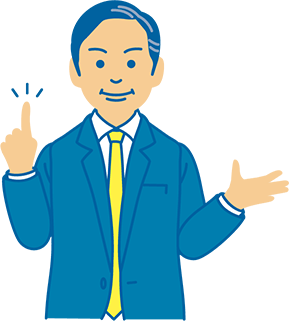
経営上の背景
外部環境要因
- ・海外メーカーや競合企業との価格競争の激化
- ・多品種小ロット生産の増加
- ・顧客からの高品質要求
内部環境要因
- ・顧客からの技術力への信頼が厚い
- ・他社で対応困難な仕事も対応可能
- ・一貫生産対応が可能
- ・生産性・収益性の低い加工部品等の受注増加による業績悪化
- ・計画的人材育成・技術伝承が進んでいない
- ・売上至上主義の傾向が強まっている
- ・生産現場の負荷管理に課題がある
解決プロセス後に得られた成果
感覚による改善から賃率による「可視化」で、業績に結びつく改善PDCAサイクルの構築と幹部社員の意識改革が実現した
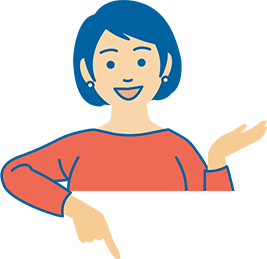
解決プロセス
「生産現場の実態把握」
目的
管理すべき数値の洗い出しと
採算性判断指標の明確化
- プロジェクト体制の構築①メンバーの選定②現状課題の共有③課題解決への方向性統一
- 工数データの洗い出し
- 賃率(人時生産性)の算出
- 受注別収益性の把握
- 生産性・収益性判断基準の明確化①必要付加価値(粗利)基準の必要賃率算定②受注別採算性判断指標
- ポイント
-
- ・事実情報に基づいた賃率の算出
- ・取引先別や受注内容グループ別の集計の実施
- ・
「生産性向上施策の策定と実践」
目的
多能工化の推進と技術承継
- 改善のPDCA実践①高リピート品の工程分解②工程別工数確認③効率向上への具体策実践④効果測定
- スキルマップ一覧の作成、属人化スキル抽出による工程の不確実要素の明確化
- スキルアップ計画の策定①個別教育②集団教育
- ポイント
-
- ・リピート率の高いオーダーを中心に工程分解を行う
- ・高い技術力を持つベテラン従業員からの個別教育体制の構築
- ・従業員別保有スキルを洗い出し、属人的スキルの伝承を行う
- ・
「継続して改善できる基盤の構築」
目的
全体最適視点からの検討体制構築と
幹部社員の意識改革
- プロジェクトメンバーによる「総合会議」体制の構築
- 製造・営業間連携強化①意見集約②接点を見つけるための改善策検討・実行
- PDCAサイクルの仕組み化・定着化に向けた検討と実践
- ポイント
-
- ・全体最適視点のPDCAサイクルの仕組み化を検討する
- ・全体最適を実現するために部門間の意識のズレを是正
- ・部署毎・部署間の認識・課題を共有化し、目標達成に向けた一体感の創出
- ・「総合会議」は、本プロジェクトの活動を継承したもの
- ・
企業概要
-
企業名
DK株式会社
-
事業内容
精密部品加工、治工具、金型の製造販売
-
資本金
20百万円
-
従業員数
42人(正社員39人)
-
売上高
535百万円(平成30年5月期)