成功事例
動作分析による作業の標準化と
生産性の向上
数値化による納得感のある現場改善
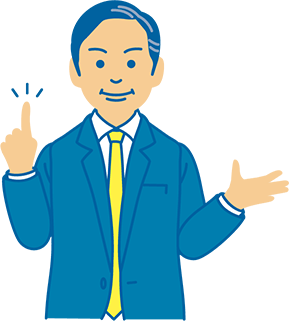
経営上の背景
外部環境要因
- ・当業界は大手ファストファッションが注目を集めている一方で国内小規模企業は低迷している
- ・当業界は流行の変化が激しく、消費者ニーズが多様化している
- ・より多様化するニーズに合ったものが売れる
- ・今後はさらにこの傾向は加速することが予測される
内部環境要因
- ・ハンドメイドへのこだわり
- ・日本有数のプリント加工の技法数と表現力の組み合わせが顧客から高評価を得ている
- ・労働集約作業型の工程が多い
- ・リーダー不在の部署が存在し、若手幹部のQCDの管理能力向上が急務
- ・経営管理全般を社長一人で管理している
- ・原価構成が不明で、個々の利益が適正かどうか判断できない
解決プロセス後に得られた成果
作業標準化を通じた現場数値の管理により、生産性目標、実績、作業状況、改善効果を見える化できた
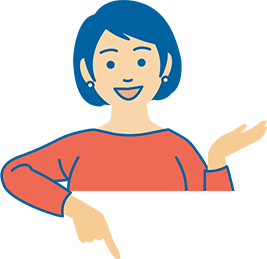
解決プロセス
「現状作業の把握」
目的
生産現場の数値化による現状把握
- プロジェクト体制の構築
- 現場改善知識の理解
- 「整理」・整頓(2S)状況の確認
- 現状作業の実態把握①作業者ごとの作業手順・作業方法の把握②作業時間計測
- 現状の問題認識の確認①作業者ごとの現状認識課題の洗い出し②作業者との改善に向けたミーティング
- ポイント
-
- ・現状把握のために生産状況の数値化を行う(時間・数量・比率・件数)
- ・
「作業標準に向けた動作分析」
目的
現場の納得感を引き出すために基準を作る
- 個人別作業手順、作業方法、段取り作業の違いの摘出と原因把握
- ビデオを使った作業の差異分析と時間計測①作業組み合わせ表(作業工程表)による作業の見える化
- 「整理」・整頓・清掃・清潔の重要性確認(4S)
- 活動計画の立案①実施案件、摘出課題の活動計画の合意
- 作業組み合わせ表を使ったムダ、作業の違いなどの明確化①4S実施と4S管理ルールの作成(現場管理の重要性理解)②個人別作業課題の明確化と改善トレーニング
- ポイント
-
- ・2Sを定着させてから、4S活動へ展開する
- ・標準作業策定は、標準的な作業方法・作業環境・作業者・速さ、適度な余裕時間に留意して実施
- ・
「作業標準化ルールの設定」
目的
数値化する仕組みを作り、生産ラインの全体最適化
- 作業手順・方法・段取り手順などの決定①製品別作業標準の決定②個別作業の作業者投入量の決定③作業標準の順守
- 設定した標準作業による実績把握と課題の摘出①作業の見える化(現場表示、作業手順書、標準帳票の整備)②作業標準の順守徹底
- 生産性改善効果の検証
- 作業の維持管理方法の標準化(ルール化)
- ポイント
-
- ・品質、生産性における目標値を設定し、現場での数値指標管理を実施
- ・改善実績評価は現場に掲示し、管理者による日々の実績チェックを行う(PDCAの実施)
- ・
企業概要
-
企業名
有限会社MS
-
事業内容
衣料品の製造加工
-
資本金
5百万円
-
従業員数
68人(正社員25人)
-
売上高
486百万円(平成30年2月期)