成功事例
VE活動実践による設計業務の標準化
製品の徹底分析で原価低減と設計標準化の実現
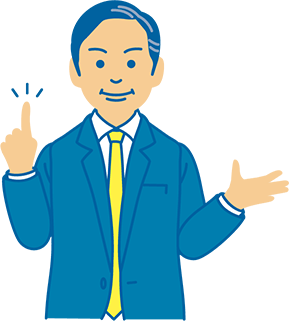
経営上の背景
外部環境要因
- ・顧客が求める価格で利益を生むためには大幅な原価低減が必要となる
- ・多様な分野でIoT活用が進展している
内部環境要因
- ・当該製品は自社が運営する事業の中でも主力であり、他事業よりも利益率が高い
- ・今後のIoT化に向けた将来性の高い事業、製品群となっている
解決プロセス後に得られた成果
原価低減・重量低減・設計能力の向上と改善プロセスにより設計部門が考える組織へと変貌した
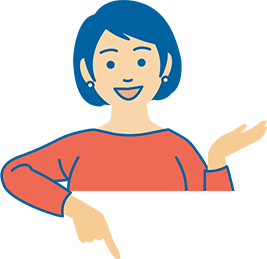
解決プロセス
「現状把握と知識理解」
目的
既存製品の現状把握とVE思考の理解
- プロジェクト推進体制の構築
- 製品別原価データの洗い出しと収集
- 原価低減余地の検討
- 対象製品の選定と顧客の要求品質の確認
- VE活動の理解①機能定義②機能評価③代替案検討(アイデアの発想・具体化案)
- ティアダウン手法の習得と実践
- ポイント
-
- ・VE活動のアプローチ方法の理解と身近な製品でティアダウンを実践しプロセスを習得する
- ・
「VE活動による原価低減、品質改善」
目的
他社製品との徹底分析による代替案の検討
- ティアダウンによる競合品比較①差別化要素や優位性の洗い出し
- 機能系統図の作成
- コストインデックス表の作成①形状②構造③工程④調達
- 改善アイデア抽出
- 製品要件の定義
- 試作品作成
- ポイント
-
- ・ティアダウン実践時、社内外のさまざまな関係者を招致し、多くの原価低減・品質改善のアイデアを得る
- ・過剰・重複・不要な機能・仕様について該当部品・材質などを抽出してコスト分析を行う
- ・
「VE活動を軸とした設計業務の標準化」
目的
自社製品間比較による部品の流用可能性とユニット化検討
- 自社対象製品の機能・仕様の抽出とコスト分析①機能系統図の作成②コストインデックス表の作成③自社製品のティアダウン実施
- 設計部品の共通化に係わるアイデア発掘・分析、評価①部品構成・材質・加工方法②部品のユニット化③モジュール化④固定・変動部位の分析
- 設計標準化構想の検討
- 設計標準仕様書の作成
- 他ユニットへ水平展開する計画の作成
- ポイント
-
- ・比較する製品を分解し、構成する部品毎に比較し、共通の要素を地道に洗い出す
- ・
企業概要
-
企業名
株式会社EE
-
事業内容
金属加工機械製造業
-
資本金
60百万円
-
従業員数
135人(正社員120人)
-
売上高
5,873百万円(平成30年12月期)