成功事例
生産量変動に対応した
省人化ラインの構築
生産ラインと出荷梱包ラインの効率化
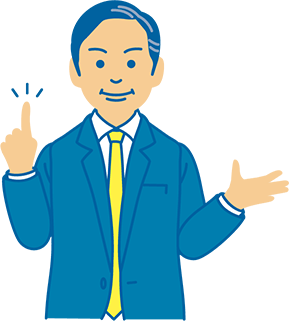
経営上の背景
外部環境要因
- ・タピオカの大流行による特需が発生した
- ・季節変動が大きい
内部環境要因
- ・大手コンビニ、洋菓子メーカーからの受注が増加
- ・OEM製品の取り扱いが300品種超
- ・多品種変量・季節変動等の受注パターン対応が必須
- ・生産性・採算性にバラつき
- ・廃棄コストが嵩んでいる
解決プロセス後に得られた成果
多品種変量・季節変動商品に対応する省人化を実現できた
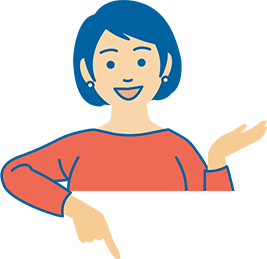
解決プロセス
「現状把握」
目的
現状分析と課題の洗い出し
- プロジェクト体制の構築
- ビジネスフロー上の各所ヒアリング
- 商品特性確認(PQ分析)
- 生産ライン稼働状況確認・人員投入量・残業状況確認
- 生産プロセス管理状況把握(3C、QCD)
- 設備管理・故障状況の確認
- 出荷梱包作業・在庫状況の確認
- ポイント
-
- ・経営者を含む関係部署参加による課題抽出とメンバーでの共有化
- ・
「生産性向上に関する課題の絞り込みと実行計画策定」
目的
課題の改善効果とスケジュール策定
- 優先課題の検討
- 改善手法・ノウハウの習得(IE改善手法、作業工程バラシ等)
- 作業改善課題共有会議の実施
- 標準作業の検討(アニュアル化)
- 作業標準の策定
- 工場管理項目検討(設備・安全・品質管理、廃棄コスト等)
- 全体工程のあるべき流れ(運搬、レイアウト含む)
- 改善計画書の策定
- ポイント
-
- ・優先順位の高い工程で改善活動を実践して効果を実感し、改善の推進力にする
- ・
「計画書に基づく改善活動」
目的
改善活動の実行と継続改善の仕組み化
- 改善活動実施に向けた推進組織づくり
- 改善活動の進捗管理
- 進捗の共有化
- 活動推進に向けた考え方・手段の検討
- 効果の検証と改善実績の標準化検討
- 継続的な改善活動
- ポイント
-
- ・改善ノウハウを蓄積しつつ、継続改善に向けた自主的ミーティングへの仕掛けを行う
- ・
企業概要
-
企業名
株式会社OH
-
事業内容
食品製造業
-
資本金
80百万円
-
従業員数
80人(正社員27人)
-
売上高
1,018百万円(平成31年2月期)