成功事例
情報共有と各工場の同期化による
全社一体型の改善活動
工場連携による5S3定徹底と
ジャストインタイム生産方式の導入準備
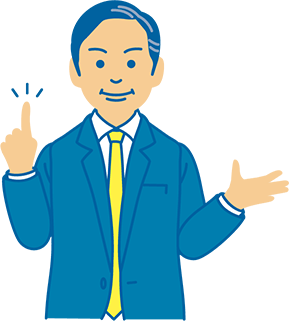
経営上の背景
外部環境要因
- ・船舶建造市場は供給過剰の状態で、製品価格が10年前の半値近くに落ち込んでいる
内部環境要因
- ・業界に先駆けて独自技術による自社ブランドのもと事業を展開
- ・メンテナンスサービスは世界20ヶ所にサービス体制を構築
- ・受注はあるが価格が合わず利益が出にくい
解決プロセス後に得られた成果
標準時間に基づく生産計画、工数計画、および実績工数集計の構築と運用が実現。一部工場では少人化生産が実現した
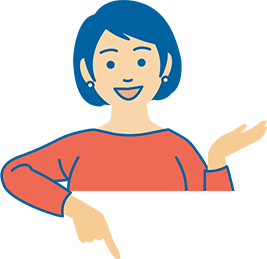
解決プロセス
「生産現場の実態把握」
目的
生産現場のムダ取り改善
- プロジェクト体制の構築①メンバーの選定②現状分析③現状課題の共有
- 改善計画策定
- 具体策の実施①5S・3定推進②停滞・運搬ムダ取り③動作のムダ取等
- 実績報告会での改善状況共有
- 他工場への横展開
- ポイント
-
- ・各工場との情報共有、同期化を目指し、全社一体型の改善活動を行う。自社に原価意識のマインドを形成する
- ・
「生産管理・原価管理の仕組みづくり」
目的
JIT生産方式の導入準備
- 標準時間に基づく生産計画の作成
- ネック工程の生産計画作成と運用
- 設計情報の活用①部品表から月別所要量算出
- ポイント
-
- ・作業日報による標準時間調査。生産計画と同期化する生産指示書を作成し、工場間での運用を行う
- ・
「原価予算の確立と運用のため組織体制構築」
目的
原価低減改善と原価管理体制構築
- 材料費の削減①調達方法の見直し
- 労務費の削減①作業時間の測定②作業分析表の作成 等
- 生産管理機能の強化①実績管理・実績原価の把握②改善策の実施
- 作業日報の活用
- 標準時間による原価管理の仕組み作り①負荷工数計画②人員計画 等
- ポイント
-
- ・作業日報の集計データを活用して工程計画を作成後、工程単位の実績工数を集計する。その集計データを活用し、標準時間に基づき原価管理へ展開する
- ・
企業概要
-
企業名
MZ株式会社
-
事業内容
船舶用甲板機械・一般機械装置の製造販売業
-
資本金
60百万円
-
従業員数
249人(正社員233人)
-
売上高
6,728百万円(令和元年9月期)