成功事例
新システム導入を見据えた
生産管理の構築による納期遵守率改善
納期対応力強化のための生産管理の
仕組みと運用の課題解決
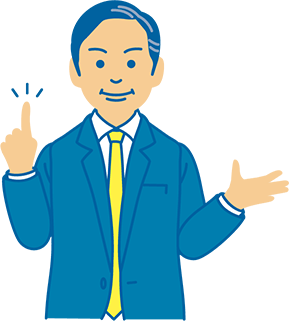
経営上の背景
外部環境要因
- ・多品種少量生産の流れで、注文は小ロット短納期ニーズが進展
内部環境要因
- ・あらゆる産業機械に使われているラックギアに強みがあり、日本トップクラスの技術
- ・年率10%以上の売上伸び率
- ・製品品種は1万点で多品種少量の受注生産
- ・生産管理が追い付かず納期遅れが頻発
- ・受注増が重なり新規受注を逸失
- ・生産指示の変更が頻発
解決プロセス後に得られた成果
業務処理の運用改善の積み重ねにより納期順守率が61%から98.4%に改善した
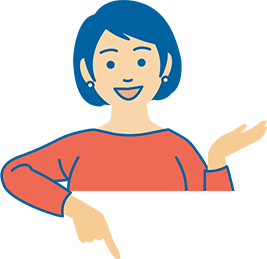
解決プロセス
「生産現場の実態把握」
目的
生産管理の仕組みの検討
- プロジェクト体制の構築①メンバーの選定②現状課題の共有
- 納期遅延の要因と状況分析
- 現状業務フローの可視化①情報の出入り②判断と伝達③情報経路と伝票の紐づけ
- 改善フロー作成
- 現基幹システムの機能・仕様の調査
- ポイント
-
- ・情報・伝票経路の全体像の見える化による全部署間の課題共有。全体最適視点により業務フローのムダを無くす
- ・
「生産計画機能の課題改善と強化」
目的
最適な生産計画立案
- 大日程計画の検討①外注先開拓・管理強化②多能工育成計画
- 中日程計画①営業情報収集(報告形式統一)②月次製販会議の実施③基準日程の納期検討
- 小日程計画①業務詳細計画立案②ネック工程の標準時間設定③総量計算
- PDCAによる計画の見直し①進捗管理体制構築
- 最適なスケジューリングシステムの調査
- ポイント
-
- ・ネック工程は、標準時間を設定後、生産の山積み・山崩しを週単位で実施して負荷を調整する
- ・
「システム構築方針の検討」
目的
現行システムの生産実態適合性確認
- 現行システムとスケジューラーの機能要件適合性確認
- システム上の課題整理
- 機能要件のとりまとめ
- RFIの作成
- ベンダー選定・評価シートの作成
- システム導入までのマイルストーン作成
- ポイント
-
- ・現行基幹システムの機能・仕様等の調査を通じて、メンバーの理解を深めながら新システム構築の方向性を検討する
- ・
企業概要
-
企業名
株式会社KH
-
事業内容
動力伝導装置製造業
-
資本金
10百万円
-
従業員数
58人
-
売上高
非公開