成功事例
あらゆるロスを削減する現場改善
既存現場の徹底した改善と仕組化により無人化工場実現への土台を整備する
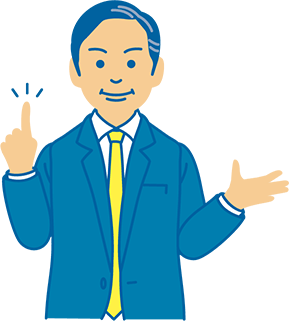
経営上の背景
外部環境要因
- ・当社の主要顧客が今後数年間で2倍の増産を計画しており、当社との取り引き量の増大が期待される
内部環境要因
- ・現状の生産システムにおいてトラブルの分析や改善が不十分な状況がある
- ・技術やノウハウの伝承が進んでいない
- ・当社は数年後にはIoT対応の無人化工場を建設し、生産性向上を目指している
解決プロセス後に得られた成果
トラブルの削減、改善プロセスの確立、年間工数の削減など、「気づいて変わる」改善風土が定着した
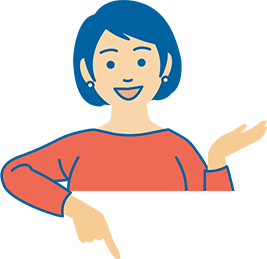
解決プロセス
「現状把握と問題整理」
目的
現状の情報共有と現場からの問題認識
- プロジェクト推進体制の構築
- なぜなぜ分析階層分析の実施
- 不具合情報のデータベース化
- 改善要素のアイデア出し
- ポイント
-
- ・現場で不具合情報を共有し改善アイデアを考える
- ・
「改善プロセスの確立」
目的
技術やノウハウの見える化と改善作業のルール化
- 作業内容の見直し
- 作業関連資料の見直し
- 作業方法のマニュアル化
- 職場管理方法の標準化
- 治具などのツールの作成
- ポイント
-
- ・属人的作業の共通化と個人ノウハウの共有やツール化で、技能の伝承や作業品質の安定化を図る
- ・
「活動進捗の見える化と改善活動教育」
目的
活動を仕組化して組織で共有し改善活動の基盤をつくる
- 活動教育の実施
- 活動板を使った進捗の見える化と情報共有
- 管理シートの作成
- 定期活動報告会の実施
- ポイント
-
- ・TPM(Total Productive Maintenance)活動に基づく当社の設備保全概念の教育と共有により定着を図る
- ・
企業概要
-
企業名
株式会社HS
-
事業内容
金属加工業
-
資本金
75百万円
-
従業員数
97人
-
売上高
2,037百万円(令和元年12月期)